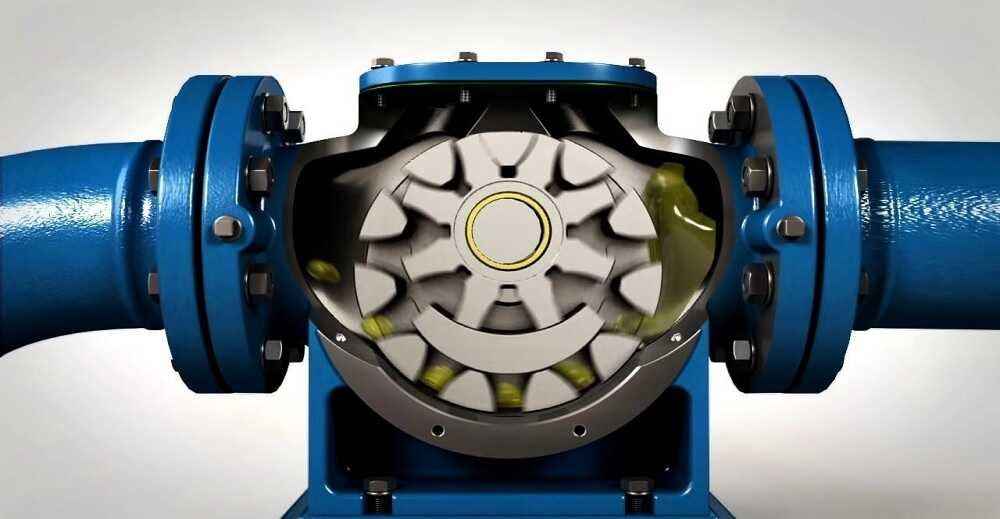
Gear pumps have been a crucial component in industrial and mechanical systems for over a century. From their humble beginnings to the cutting-edge technologies we see today, the evolution of gear pumps has paved the way for revolutionary advancements across industries. Their versatility and reliability make them a critical solution for transferring fluids in applications ranging from automotive to manufacturing processes—and beyond.
This blog explores the fascinating history of gear pumps, their working principles, innovations, and how rotary gear pumps are shaping modern industries. Whether you’re an engineer, a business owner, or simply curious about industrial pumps, here’s everything you need to know about the evolution of gear pumps.
A Brief History of Gear Pumps
The First Gear Pump
The invention of the gear pump dates back to the late 16th century when it was introduced by German engineer Johannes Kepler. Designed as a simple solution for moving fluids, the gear pump used interlocking gears to create pressure and facilitate the movement of liquids. Although rudimentary by today’s standards, it revolutionized fluid transfer in its time.
Kepler’s design was basic but functional. Early prototypes relied on manually powered or small steam engines to drive the gears. These pumps were used primarily in small-scale applications, such as draining mines or lifting water for irrigation.
Early Industrial Applications
With the Industrial Revolution in the 18th and 19th centuries, gear pumps found growing applications in industries like textile manufacturing, steam engine operation, and chemical processing. Their ability to provide consistent and controlled flow rates made them invaluable in systems requiring precision and reliability.
Advancements in metallurgy and machine tooling during this period allowed for the manufacturing of higher-quality gears and housings, leading to longer-lasting and more efficient pumps.
The Advent of Rotary Gear Pumps
The 20th century saw the development of the rotary gear pump—a design innovation that brought gear pumping to the forefront of modern engineering. This pump’s compact design allowed for handling more viscous fluids, making it a game-changer for oil, fuel, and high-viscosity liquid transportation.
Rotary gear pumps quickly became the go-to solution for applications requiring durability and reliability under more demanding conditions.
The Inner Workings of Gear Pumps
Essential Design Principles
At the heart of a gear pump lies its intermeshing gears, often two or more. These gears rotate in opposite directions within a tightly sealed housing. This design creates suction at the inlet and pressure at the outlet, enabling fluid to move steadily through the system. Unlike centrifugal pumps, gear pumps excel in maintaining a consistent flow rate, regardless of changes in pressure.
Key Components of Gear Pumps Include:
- Housing: Provides the casing where the gears rotate.
- Gears (external or internal): Drive the fluid movement.
- Shafts and Bearings: Offer support and stability for smooth operation.
- Seals/Gaskets: Prevent fluid leakage while maintaining pressure integrity.
Rotary Gear Pump Innovation
Rotary gear pumps differentiate themselves by using closely aligned gears and a smaller profile. These pumps are particularly beneficial for handling specialty fluids, including adhesives, oils, and slurry-like materials that would challenge other pump types. Modern rotary gear pump designs have also integrated advanced sealing technologies to extend service lifetimes while reducing maintenance needs.
Modern Innovations in Gear Pumps
Materials and Durability
One of the most significant advancements in gear pumps has been the introduction of new materials—ranging from corrosion-resistant stainless steel to high-performance thermoplastics. These materials improve resistance to wear, corrosion, and extreme temperatures, making gear pumps more versatile across industries such as pharmaceuticals, food processing, and petrochemicals.
Digital Integration and Smart Systems
The rise of IoT (Internet of Things) and smart manufacturing technologies has brought digital integration into the gear pump landscape. Many modern industrial pumps are now equipped with sensors that monitor real-time performance indicators like flow rate, vibration, and temperature. These smart systems not only help identify maintenance needs early but also optimize energy efficiency and reduce overall operational costs.
Enhanced Efficiency
Recent innovations include reduced power consumption designs, improved gear alignment, and faster priming times. Gear pumps are now more energy-efficient, contributing to cost savings and environmental sustainability.
Customization for Niche Applications
Custom-engineered rotary gear pumps are increasingly catering to niche applications. From micro-pumps in medical devices to large-scale industrial pumps moving petroleum products, companies are leveraging modular designs to create tailored solutions.
Applications of Gear Pumps Across Industries
The versatility of gear pumps allows them to operate effectively across a wide range of industries:
-
Automotive
Gear pumps play a vital role in automotive manufacturing, particularly in fuel injection systems and lubrication circuits. Rotary gear pumps are unparalleled when it comes to handling engine oils with precision.
-
Pharmaceuticals and Biotech
The pharmaceutical industry relies on gear pumps for liquid transfers that require sterility and precision. Applications include the transportation of syrups, vaccines, and liquid pharmaceuticals in controlled environments.
-
Food & Beverage
Gear pumps are extensively used in processing viscous liquids like chocolate, syrups, sauces, and edible oils. Their ability to preserve product integrity makes them perfect for such sensitive applications.
- Energy & Petrochemicals
Gear pumps are widely used in the oil and gas industry for pumping crude oil, fuel, and other hydrocarbon-based liquids. They perform exceptionally well under challenging conditions like high pressure and extreme temperatures.
-
Chemicals & Adhesives
Rotary gear pumps excel in handling viscous substances such as adhesives, resins, and industrial chemicals with ease, ensuring continuous flow and reducing material waste.
Why Gear Pumps Remain Industry Favorites
Since their inception, gear pumps have continually proven themselves as reliable technology in fluid handling systems. Here’s why businesses trust them:
- Consistency: Gear pumps provide a steady and controlled liquid flow unparalleled by other pump types.
- Durability: Robust designs and the use of high-quality materials ensure a longer lifespan.
- Versatility: Their ability to handle a wide variety of fluids makes them suitable across industries.
- Compact Design: Rotary gear pumps offer power in a small footprint, simplifying integration into systems with limited space.
- Low Maintenance: Modern innovations ensure minimal service interruptions and faster troubleshooting.
Choosing the Right Gear Pump for Your Business
Selecting the right pump depends on your specific requirements. From fluid type and viscosity to operating conditions and flow rate, every detail matters. Working with a knowledgeable supplier or manufacturer can make all the difference in identifying the optimal solution.
For businesses looking at modern rotary gear pumps or other industrial pump options, investing in up-to-date technologies not only ensures operational efficiency but also positions your organization for long-term success.
Gear Pumps Powering the Future of Industries
From Johannes Kepler’s early designs to today’s innovations in rotary gear pumps, gear pumps have evolved to meet the demanding needs of modern industries. They exemplify how engineering excellence continues to drive advancements in universal technology.
Whether you’re in manufacturing, energy, or even food production, understanding the capabilities of modern gear pumps can unlock new efficiencies for your business.